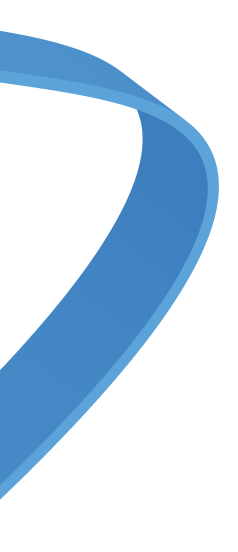
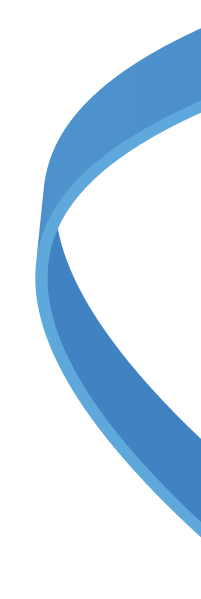
Drum Covering Rubbers
Assembly is carried out on site and while the drum is on the conveyor. It is a complete coating of wear elements, used to protect the drum on which it is placed and to improve its performance. 12 mm thick profile structure, hot vulcanized on a 2 mm thick stainless steel or Corten steel surface. The 14 mm thick structure molded in this way is produced in a standard length of 1830 mm and in two different widths: 135 mm (symbol “S”) or 142 mm (symbol “L”). These are offered according to the diameter of the drum to be coated
-Density: 1.15 – Flexible: 55° +/- 5° Shore A.
-Anti-oil black rubber
Parablond rubber Shore A at -1.05 density and 40° +/- 5° hardness: Ultra flexible, good shock absorption.
Chlororoprene rubber with non-flammable and anti-static properties.
The sliders serve as the sliding surface for the SLIDE-LAG® bars. They are welded onto the drum once and for all: SLIDE-LAG® bars slide between the two sliders and can be easily replaced with new ones. Double or single sliders are also available in standard lengths of 1830 mm. The 2 mm thick sliders are available in stainless steel and Corten steel.
EDGE-CROWN element: 250 mm long piece with a length of 135 mm (symbol “S”) or 142 mm (symbol “L”) in a vulcanized, anti-abrasion black rubber profile. These elements, placed at both ends of the drum, with progressively decreasing thickness, allow for better centering of the belt.
BOR element: 250 mm long part, molded in lengths of 135 mm (symbol “S”) or 142 mm (symbol “L”), made of special anti-abrasion red rubber, smooth surface, without structure. Wearable elements located at the ends of the drum. They allow the replacement of a complete row to be avoided, replacing the end parts only when they wear out.
Although SLIDE-LAG® is a replacement part, we were asked to develop a part with a higher thickness.
Although SLIDE-LAG® is a replacement part, we were asked to develop a part with a higher thickness.
“Small size”, because they are vulcanized in 510 mm length (instead of 1830 mm). But they are “strong” because they are obtained with a rubber thickness of 16 mm (instead of 12 mm). This is how the lifetime of a part is extended.
Each SLIDE-LAG® rod is centered according to the diameter of the drum: This indispensable process ensures that the bar perfectly matches the diameter of the drum and allows it to be held and slid under the sliders.
Except in a few rare cases (tape not taut enough, drum diameter not suitable for the system), the lifetime of the SLIDE-LAG® coating is one of the longest of any commercially available drum coating system. It is not uncommon for a SLIDE-LAG® coating to be used for ten years. However, this is only if they are installed on installations that operate only a few hours a day.
The lifetime we observe most often is 6 months to 5 years. At 6 months lifetime, the working conditions are harsh and the belt rotates 24/24. At 5 years lifetime, conditions are what can be considered “normal”, i.e. the belt runs 5 days and stops 2 days.
The lifetime of a SLIDE-LAG® coating can be affected by many factors: Improper calibration to the diameter of the drum, poorly adjusted belt tension, frequent and momentary shutdowns/starts.
Separation of the rubber from the steel surface is extremely rare or even non-existent. There is no cold bonding of the rubber onto a steel surface. The SLIDE-LAG® coating is a raw mixture that we cook: The cooking time is 12 to 25 minutes. The steel surface is degreased, sandblasted, on which two adhesives are applied which, during baking (or vulcanization), ensure that the coating becomes one body with its surface. The four sides of the coating are meticulously checked.
Supports drum/tape adhesion, protects the tape;
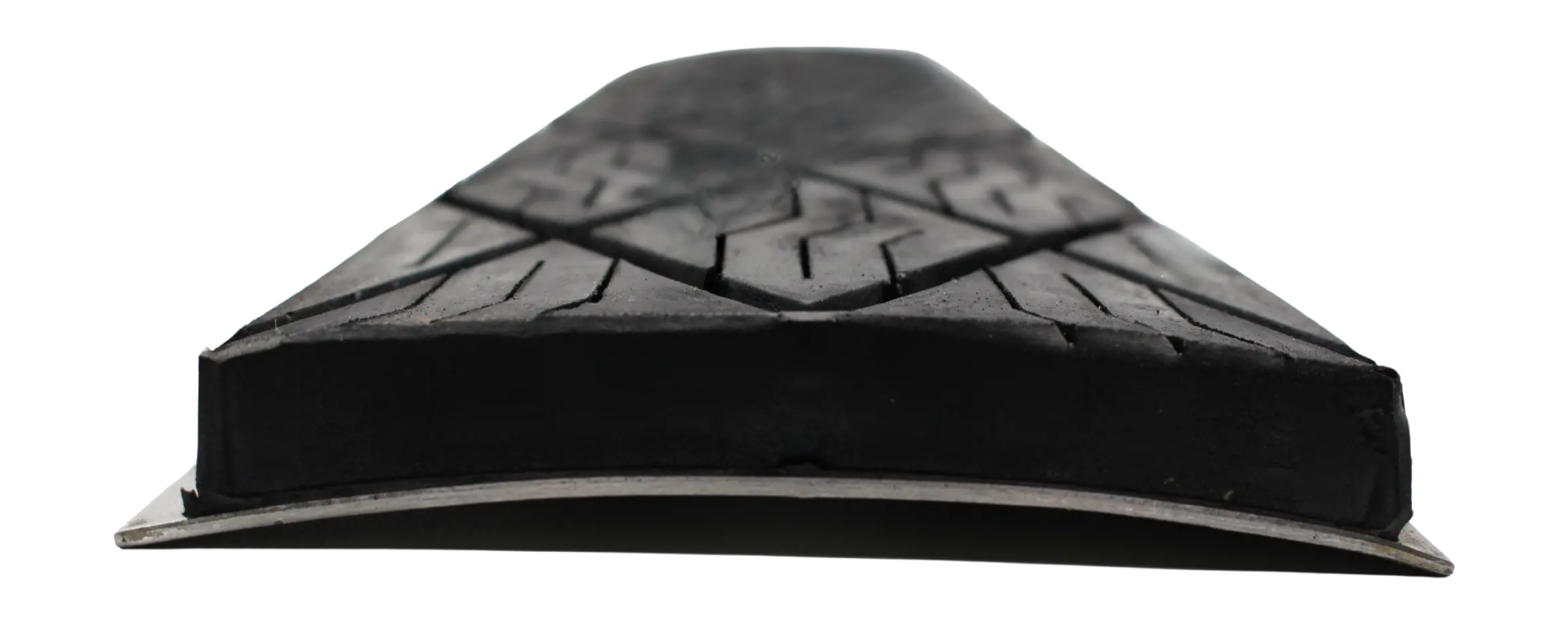